Thursday 13th March 3hr 15min
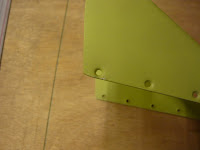
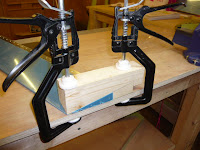
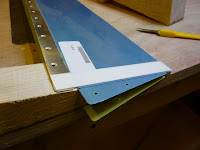
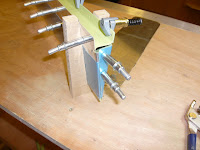
Ordered replacement R710. Made new blocks. Practiced and then completed trim tab end bends. Match-drilled end tabs. Assembled bending break and completed trailing edge bend.
I found that I had edge distance problems with the R-710 rudder brace, as can be seen from the photo. This happened because I didn't like the half holes left after trimming off the cheeks and I ground down the edges until they were completely gone. The cut lines are supposed to go between the CENTRES of these guide holes. Fortunately, I had left the spray booth in place so it was not difficult to prime up the new part.
The infamous trim tab end bends went much more smoothly this time. Firstly, I made much wider blocks to hold the skins for the bend. Secondly, I used double-sided tape (the white take in the photo. to make sure the skins stayed put in the blocks while the bending was going on. Thirdly, I left out the rivet gun shown in the manual and made the bends by pushing on the tabs with a piece of scrap wood. The resulting bends could be a little sharper but they are in the right place at least and they don't look as if they were beaten with a crow-bar.
I wouldn't use that particular type of double-sided tape however. It consists of a thin layer of foam with a glossy paper layer on each side that you pull off when you are ready to use it. The problem is that the glue is much stronger than the foam tape itself and it was really difficult to get off, particularly inside the trailing edge where access was difficult.
No comments:
Post a Comment