New Tools!!!
Picking up the pieces
Match-drilled reinforcing plates W-907B, C, D and E to the W-907A left and right aft spars. Deburred and edge-prepped all parts. Cut aileron push rod openings in W907D left and right. Countersunk W907C per plans. Dimpled W-907A top flange in way of W907D doubler fork.
However, what did make me scratch my head was that I seemed to be missing several pre-punched holes on the spar. These holes are for rivets to attach the lower edge of the flap and aileron gap fairings, where they join the W907-D (mid-span) and E (outboard) doubler plates (not the W-907C - its holes are all present and correct). The plans show all six of these holes but they do not exist on the spars and therefore can't be match-drilled through the doubler plates along with the rest. The holes are all pre-punched on the gap fairings themselves so the only option appears to be to match-drill them in assembly with the doubler plates and aft spar using the fairing holes as a guide. I could have done this on the spot but I thought it might be better if the fairings could be clecoed to the skins at their top edge as well as to the spars at their lower edge. In this way, I can be certain that these tabs are hitting the doubler plates at precisely the right point. I better put it on a 'to-do' list so that I don't forget it while the top skins are on for match-drilling.
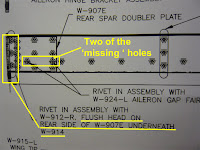
Vans comes through
Vans agree to ship new spars
It turned out that Terry Elgood changed his mind and regrets not getting new spars. Waves and mismatches between skin edges appeared on his wings only after riveting on the skins - even though the spars had appeared perfectly straight after the re-bending operation. Also, my Inspector Mick Bevan was not very happy about trying to fix such a major part 'in the field'. I pointed this out to Ken Scott and also said that it was important to me that any flaws in my plane should be my own fault and not anybody else's.
Having made my case, and after a short period of reflection, Ken came back and said they would replace the spars. Maybe it was no more than my rights but I still felt great that Vans had stood by me and honoured their side of the bargain. The mark of a truly great company is not that things never go wrong but how well they respond when problems do arise. Clearly Vans are a great company.
Only trouble is that I am going down with a stinking cold; two days before the annual SAAC fly-in and a Michael Bublé concert (separate event - our fly-ins are rather more low-key) next Saturday.
Wing spar bender
Riveted platenuts to bottom flange of left wing spar. Found major manufacturing fault. Contacted Vans.
I went back to work on the wing spar this evening and completed riveting all the platenuts on the bottom flange of the left spar, including the #6 platenuts for the three inspection plates.
When you have got a lot of anything to do, I find it better to break it down into its parts and approach it production-line style. For example on this job, rather than making a separate job of each platenut, I did all of them together following these steps:
- Cleco one 'lug' of every platenut in place.
- Put rivets in the other lug of every platenut.
- Squeeze all of these rivets.
- Replace the clecos with rivets in the 2nd lug of each platenut and
- Squeeze these rivets.
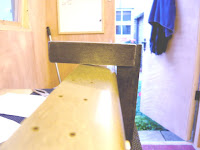
I remembered an article on page 10 of the latest RVator, telling the story of Terry Elgood, a Canadian builder who had the same problem. Terry fixed his spars by cutting a notch in the end of a length of oak and bending the flange back to its proper position by using putting the notch over the flange and levering it, little by little, working up and down along the length of the spar moving only an inch or less at a time.
I am deeply suspicious of this. I can't see how you can get a straight flange out of this procedure as the lever is exerting a point load on a very short section of flange at a time. In fact I think I see some waves in the lip of Terry's flange in the photos but the resolution is not high enough to be sure. I remembered thinking how convenient for Vans if builders, especially those at a great distance from Aurora, would be so good as to fix Vans quality problems and save them from shipping expensive replacement parts to the four corners of the globe.
Before hysteria took over, I rang Vans support and Ken answered. He was sympathetic of course and embarrased that it had happened but basically he is happy that Terry Elgood's method makes the issue go away and its up to me to implement it. To be fair, he said they would "make it right" whatever that means. However, I couldn't make him say that he would replace the spars if the repair went wrong. I have to think about this some more.
NOT a good day!
The shock of the Big!
Completed inventory and storage of wing kit. Countersunk left wing for tank attach and inspection plates
I finally finished the inventory by going through the long narrow pieces such as tubes, angles, spars, fairings and so on. - Every piece of the kit was present and correct. It is quite a juggling act now to get everything properly stored above the rafters of the shop. When the wings are completed, I am going to have to put in a second 'deck' up there. The design of the shop included enough head-room below the rafters to allow the wings to be slung there if necessary. However, they would restrict access to the area above and I would need to re-locate the light fixtures to the walls so I would rather not avail of that facility.
The platenut rivet countersinks went without a hitch. However, the countersinks for the #8 screws were a bit of a shock. They are far bigger than any countersink I have done so far. Also, they greatly expand the size of the existing pre-punched hole and they totally disregard the idea of leaving a cylindrical portion of the hole, which I had thought was important. These countersinks go all the way through the material - and then some! The justification lies in the fact that we are talking about screws here rather than rivets and the load is more than adequately spread by the platenut. If we were dealing with a big rivet in these holes then countersinking to this depth would not be acceptable. However, it comes as something of a shock to be putting such big countersinks into this beautiful spar, but you just have to get on with it.
To check that the countersink was the right size, I used the dimpled test piece method rather than the sawn off #8 screw head as mentioned in the manual. I set the countersink cage depth using trial holes in a piece of waste before touching the spar itself. However, if you are doing the same, just make sure that your test piece is not 'dished' around the dimple and that it is otherwise flat in all directions. Otherwise, your tester will 'rock' from side to side even when the dimple is fully seated in the countersink, fooling you into thinking that you need to cut deeper. I think this was what got me into trouble on the equivalent dimples on the HS spar. No problem this time, however and I was very happy with the countersinks I produced.
My method was to:
- drill out the screw holes in the flange (not the rivet holes!) to #21,
- prepare a guide piece with a #21 hole in it (actually the offcut from the angle used for the HS attach brackets),
- use the drill bit shank to centre the guide piece on the spar flange hole and clamp the guide piece to the flange with the drill bit still in place.
- Now I was able to go ahead and countersink to the required depth knowing that my countersink would be centred on the hole, perfectly formed and to the correct depth - result!
Beware that the platenuts for the inspection plates on the bottom flange are smaller than those for the tank skin attach platenuts. The screws along here (4 platenuts at each of 3 locations) are #6, for which #30 is the correct cutter. I don't understand why they call out #40) I still used a guidepiece with a #30 hole as I didn't want to change a winning formula. Having some guide material left with a hole the exact same as the cutter guide pin is essential, otherwise the cutter will wallow around once it breaks out the other side of the flange and starts to enlarge the hole.
I used an artists' brush to spot-prime all the countersinks. I intended to just wipe off the excess but it dried so fast that I couldn't . However, a stanley knife blade worked perfectly with no effect on the anodised flange surface- just like scraping paint off glass after painting a window.
Work was slow today. I expected to get both spars done and the platenuts actually riveted on. The slowness was partly because I had been on a long lay-off from building. I spent longer than I should have foostering around with setting and re-setting the countersink cage. I have two of them, specifically to cut down on re-setting, but three would have been better because I want to keep one permanently set for #40 countersinks at all times and the other was being changed between #30 and #21. If I get another, I can leave it permanently set for #30 and use the third for all other sizes.
Wings unfurled
Wing kit Inventory
To protect the skins further, their bottom edges are resting on a piece of cardboard and they also have a sheet of cardboard between them and the wall and another between them and the crate top.
They certainly need protection because, I managed to ding up the corners of two bottom skins next to inspection holes while I was building this storage. It is only a small ding and I should be able to make it dissapear before I hang the affected skins but I have no idea how it happened, except that I am certain they were perfect when I first opened the box. Be careful how you handle your skins. Preferably get someone to help you with them because they are big and floppy and delicate.
Rudder Rolling
Rolled and riveted leading edge of rudder. Put in rivets at narrow end of elevator end ribs. Pop-riveted ribs at narrow end of rudder tip rib.
With a clean shop, I set about finishing off all the left-over jobs from the empennage before settling down to the wing construction phase of the project.
Ultimately, however, there just is not enough space in there to set both rivets in the last position, so I had to content myself with pop-rivets on the underside of the elevators and on both sides of the rudder.
First day of 'real' building since the break - and very enjoyable it was too.
How did the shop get this dirty?
Tidied up the Shop
During the nearly 10 week lay-off from the project, I was constantly in and out of the shop to find some tool or other that I needed for the re-modelling job. Apparently, I was not especially tempted to linger, or run a loving finger over the finished emp parts, or even put things back properly.
Consequently, the untidy mess that greeted me when I finally got to begin the wing construction was amazing. It took a solid two hours of sorting out aircraft from non-aircraft bits and tools and putting them away before it looked like a place of work again.
If you think I am going to publish a photo of the state it was in, then think again! I'm not proud of it.
Look at those Tanks!
Unpacked, examined and stored pre-built tanks
The workmanship is first class. Check these pictures against most other builders' websites and you can see the difference straight away. The most obvious difference is that Evan has obviously sold his soul to somebody he shouldnt, in exchange for the sacred knowledge of how to do tank sealant neatly. Just as importantly, you will never see better riveting. However, just as Persian rug makers deliberately include a mistake in their delicate patterns because only God is capable of perfection, I noticed just one rivet marked "oops".
Wings arrive!
Accepted wings delivery
Despite requesting one, the truck had no tail lift and I certainly have no cargo handling equipment at home. As it turned out, the driver was more than willing to help. The length of the spar box is an advantage because it is easy to lift just one end down from the 4 ft 6in deck of the truck and then lift the other end. The main box was quite a bit lighter than I had expected (the sizes and weights are all on the Vans website) because of course the parts for the tanks were missing from it.
With the boxes on the street, the truck departed. My advance planning for this situation amounted to buying two 'skates' for moving heavy furniture or appliances. Dorothy and I were about to use these to move the boxes towards the house when a kindly neighbour came along and insisted on lifting them with me. He is retired and a good 10 years older than me and I fully expected him to damage his back but there was no stopping him. I often come across situations like this where I carefully plan how I am going to handle something and someone comes along and takes over, dismissing my plans with "No, no, you don't want that. You want this". It always seems impolite to burst the baloon of their well-intentioned 'expertise'.