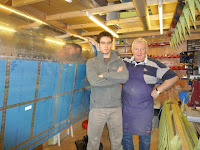
I certainly intend to bring the blog right up to date at some point, probably in the break between finishing the wings and the arrival of the fuse kit. I am also considering moving to a website of my own. However, for now, I will just post a bulletin to summarise where I am at present.
On new years’ day, with the help of my son, Conor, I began to rivet on the top skins of the first wing (the right hand one). We finished up the job on the following day.
Looking back over the year, I see from my diary that I have worked a total of 501 hours and 37 minutes, which is astonishingly close to my target of 500 hours per year. I worked on 125 days (roughly every third day) so the average time worked was therefore 3 hours and 40 minutes. However, as you might expect, this divides down into evenings of 2-3 hours and full days of 6-9 hours.
In total, I have now spent 609 hours,12 minutes on the project, of which 280 hours 35 minutes were on the empennage and 326 hours,37 minutes so far on the wing. These figures do not include breaks, time spent buying supplies or time spent researching the forums or other builders sites to see how they approached each task.
I seem to be slower than other builders but that is no harm, especially if it results in good workmanship and a nice result. I am also enjoying the process immensely and I attribute this partly to still being a non-pilot. I think that flying or training to fly would distract me from the project as well as diverting money from it. Be assured, I do want to fly. In fact it is the stuff of my daydreams. However, for the moment I am very content with building.
There still isn’t a schedule for the rest of the project. All I have is some loose 'expectations’. For instance, I expected to have finished the wings at this stage but they won’t now be finished until sometime in February or March. The fuse is now on order and will arrive during March so that should be finished in the spring of 2010.I plan to begin training at that stage, while working on the finishing kit. All going well, I should spend 2011 and spring of 2012 on engine, wiring and systems and move the plane to an airfield for assembly and painting duriing the summer of 2012 with first flight happening late that summer. Now all I have to do is work out how to afford it all.